Careers
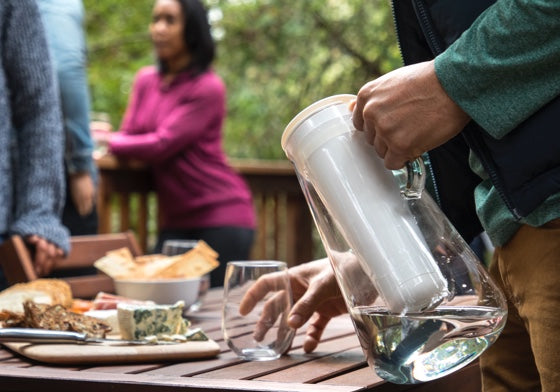
-
open positions
-
Senior Quality Manager
Position Summary
LifeStraw is looking for a Senior Quality Manager to join the team! You will be responsible for the planning, coordination, implementation, and reporting of all Quality related activities from all nominated suppliers and finished-goods manufacturers and all the 3pl warehouses, such that their deliverables meet all required specifications and that these goods ensure the successful on-time and first-quality production of LifeStraw's finished goods.This position will report to the Director of Production and will be based out of our office in Baltimore, Maryland.
Key Responsibilities
Develop and implement the quality control systems (specifications, procedures, fixtures, and quality KPI's) with South Korean manufacturing suppliers and partners to prevent deviation in production:
* Identify the processes' risks and weaknesses regarding to product quality requirements and implement preventive actions and quality controls plan accordingly (e.g., SPC, Poka Yoke…).
* Validated industrial pilot production finish-goods before full-scale production release to validate the product and process manufacturing capabilities (Industrial green light).
Implement QMS process
* Identify the processes' risks and weaknesses regarding to product quality requirements and implement preventive actions and quality controls plan accordingly (e.g., SPC, Poka Yoke…).
* Implement supplier quality APQP processes that drive zero defect launch of new products.
*In conjunction with suppliers, identify potential failure modes during the launch process and implement countermeasures to prevent them.
* Track and analyze supplier quality data, internal and external, to determine additional controls that need implemented to maintain quality standard.
* Perform quality system audits at vendors and in conjunction with them toward closure of identified system weaknesses.
Monitor the quality compliance of regular productions:
* Drive regular and ad hoc suppliers' audits on-site to check production and quality control plan compliance and check non-Conformity corrections when required.
* Monitor engineering changes and quality indicators from suppliers and continually improve quality though-out all processes, suppliers, and finished goods, manufacturers.
* Evaluation of vendors through QCGOAL Data & system audit.
* Report monthly the KPIs to the Operations, Production and Quality management.
* Provide evidence of quality system compliance upon request (e.g., for Public Health tenders).
* Ensure that the Manufacturer completes production on time and provides the Certificate of Quality and Certificate of Analysis to the Supply Chain team before shipment.
Manage continuous improvements through customer complaint feedback:Monitor customer claims database.Lead the research and troubleshooting of customer claims to reach 'zero customer complaint standard' as directed.Manage, coordinate, and validate product and process Design Changes promptly.Extrapolate learnings and disseminate best practices to prevent potential occurrences of similar issues on comparable products and processes.Identify and propose opportunities for product enhancements and process improvement towards lean manufacturing targets: shorter lead time, reduced inventory, products, and process costs optimizations.
Key Competencies
ISO 9001; 2015 and IATF 16949 system implementation experience.Knowledge of 5 Core Tools (APQP, PPAP, Control Plan, SPC & MSA).Supplier quality management.A pragmatic approach, 'hands-on' attitude.Display an organized, comprehensive, and data-driven approach to problem-solving.Problem-solving mindset: team spirit style that encourages results-driven, task-oriented collaboration.Fast response and adjust quickly to changing conditions.Can work under pressure.Multiple projects management.Excellent in communication and interpersonal skills.Willing to work across multiple time-zones.Self-disciplined and drive, task-focused, self-confidence to compel corrective actions from suppliers,Willing to travel as authorized.
Experience & Education
Master or bachelor’s degree in Engineering / Quality or equivalent pragmatic technical experience in an industrial environment.Minimum 8 years of a proven QMS implementation and quality control experienceProven track record of successful quality system implementation and management, product launch, and scale-up in production.Proficient in 5 core QC tools, Lean-Six Sigma, and FMEA techniques.Familiar with mass production in various products like plastic Stainless steel and assembly processWater filtering or filtering membrane production knowledge will be an asset
If you possess the above qualifications and the drive to meet the challenges, please send your resume/CV to jobs@lifestraw.com, including day-time telephone contact and names and email contacts of three references. We will only respond to electronic applications and to shortlisted applicants.LifeStraw believes that diversity, equity, and inclusion is critical to our success. We are an equal opportunity employer whose team works hard to build respect, dignity, and equity into everything we do. We seek to recruit, develop, and retain the most talented, driven, and entrepreneurial minded people from diverse backgrounds and experiences. If you are interested in opportunities, please send your resume/CV tojobs@lifestraw.com